All about Alcast Company
All about Alcast Company
Blog Article
Get This Report on Alcast Company
Table of ContentsFascination About Alcast CompanyThe 45-Second Trick For Alcast CompanyTop Guidelines Of Alcast CompanyThe Single Strategy To Use For Alcast CompanyThe Single Strategy To Use For Alcast CompanyThe Definitive Guide for Alcast Company
Chemical Contrast of Cast Light weight aluminum Alloys Silicon advertises castability by reducing the alloy's melting temperature level and enhancing fluidness throughout casting. Additionally, silicon contributes to the alloy's toughness and wear resistance, making it useful in applications where longevity is essential, such as automotive parts and engine elements.It also improves the machinability of the alloy, making it simpler to refine into completed items. In this means, iron adds to the total workability of light weight aluminum alloys.
Manganese contributes to the toughness of light weight aluminum alloys and improves workability. Magnesium is a light-weight element that provides strength and influence resistance to light weight aluminum alloys.
Some Known Factual Statements About Alcast Company
Zinc enhances the castability of aluminum alloys and helps manage the solidification procedure during casting. It enhances the alloy's toughness and firmness.

The primary thermal conductivity, tensile stamina, yield toughness, and prolongation vary. Select suitable raw products according to the performance of the target product created. Amongst the above alloys, A356 has the highest thermal conductivity, and A380 and ADC12 have the most affordable. The tensile limitation is the opposite. A360 has the most effective yield stamina and the highest possible prolongation rate.
Alcast Company - Truths
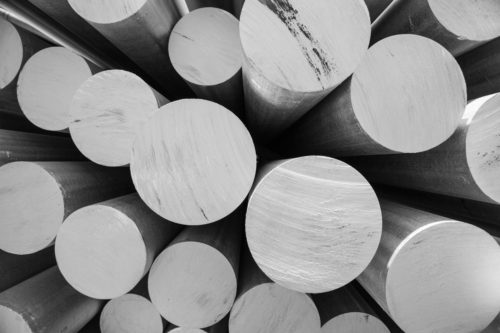
In accuracy casting, 6063 is appropriate for applications where intricate geometries and top notch surface area coatings are vital. Examples include telecommunication rooms, where the alloy's premium formability permits for smooth and visually pleasing layouts while keeping architectural integrity. In the Lighting Solutions sector, precision-cast 6063 components create classy and effective illumination fixtures that call for detailed shapes and great thermal performance.
It causes a better surface area coating and much better click this link rust resistance in A360. Furthermore, the A360 shows remarkable elongation, making it ideal for facility and thin-walled elements. In precision spreading applications, A360 is fit for markets such as Customer Electronic Devices, Telecommunication, and Power Tools. Its improved fluidity enables elaborate, high-precision parts like smartphone coverings and interaction gadget housings.
Excitement About Alcast Company
Its one-of-a-kind buildings make A360 a valuable option for precision casting in these sectors, improving item resilience and quality. Casting Foundry. Light weight aluminum alloy 380, or A380, is an extensively made use of spreading alloy with several distinctive attributes.
In precision spreading, light weight aluminum 413 radiates in the Customer Electronic Devices and Power Devices sectors. It's generally used to craft complex elements like smart device housings, cam bodies, and power device coverings. Its accuracy is remarkable, with limited tolerances up to 0.01 mm, making sure flawless item assembly. This alloy's remarkable rust resistance makes it an exceptional selection for outside applications, guaranteeing resilient, durable items in the stated sectors.
The Ultimate Guide To Alcast Company
As soon as you have actually chosen that the light weight aluminum pass away casting procedure is appropriate for your job, a vital next action is choosing on one of the most proper alloy. The aluminum alloy you choose will considerably influence both the casting procedure and the properties of the final product. Due to the fact that of this, you need to make your decision very carefully and take an educated approach.
Determining the most appropriate light weight aluminum alloy for your application will imply weighing a large array of characteristics. These comparative alloy qualities adhere to the North American Die Spreading Association's standards, and we've divided them right into 2 groups. The initial group addresses alloy characteristics that influence the production process. The 2nd covers attributes impacting the homes of the final product.
Little Known Questions About Alcast Company.
The alloy you choose for die spreading directly impacts several aspects of the casting process, like how easy the alloy is to deal with and if it is susceptible to casting issues. Warm cracking, also understood as solidification splitting, is a common die casting defect for aluminum alloys that can cause internal or surface-level rips or fractures.
Specific aluminum alloys are a lot more prone to warm cracking than others, and your choice needs to consider this. Another common issue discovered in the die casting of aluminum is die soldering, which is when the actors stays with the die walls and makes ejection tough. It can harm both the cast and the die, so you need to look for alloys with high anti-soldering residential or commercial properties.
Rust resistance, which is currently a remarkable attribute of aluminum, can vary substantially from alloy to alloy and is a crucial characteristic to take into consideration relying on the environmental conditions your product will be exposed to (Casting Foundry). Wear resistance is one more residential property generally looked for in aluminum products and can separate some alloys
Report this page